The Rise of Digital Twins in Industry
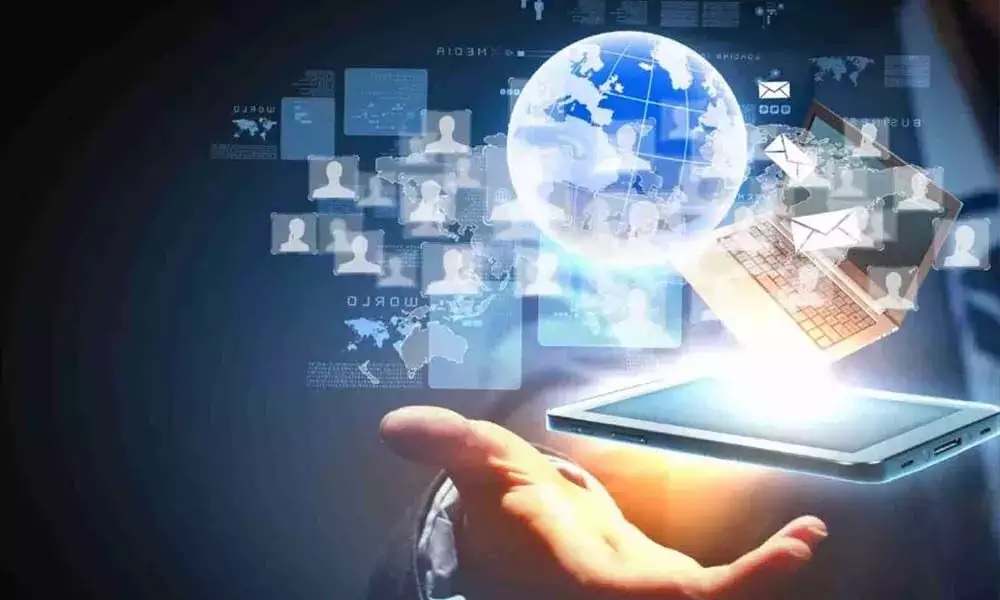
The concept of digital twins has been around for a while, but it is only recently that it has gained popularity in the industrial sector. Digital twin technology is a virtual replica of a physical asset, process or system that can be used to simulate and analyze real-world scenarios without the need for physical testing. This technology has the potential to revolutionize the way industrial organizations operate.
What is a Digital Twin?
A digital twin is a virtual representation of a physical asset, such as a machine, factory, or even an entire system. It uses real-time data from sensors and other sources to create a model that can be used for simulations, predictions, and analysis. Digital twins can be used across many industries, including manufacturing, aerospace, healthcare, and more.
How Digital Twins Work
To create a digital twin, a physical asset or system is first equipped with sensors that collect data about its performance, condition, and other relevant parameters. The data is then transmitted to a cloud-based platform where it is processed and used to create a virtual model of the asset or system. This model can then be used to simulate different scenarios, test new configurations, and predict future performance.
For example, in the manufacturing industry, a digital twin can be used to simulate the performance of a production line, predict maintenance needs, and optimize overall efficiency. In the healthcare industry, a digital twin can be used to simulate the effects of different treatments on a patient, predict outcomes, and optimize care plans.
The Benefits of Digital Twins
Digital twin technology offers many benefits for industrial organizations, including:
- Improved Efficiency: Digital twins can be used to optimize the performance of assets and systems, reducing downtime and improving efficiency.
- Better Predictive Maintenance: By monitoring real-time data, digital twins can predict maintenance needs, reducing the risk of unexpected downtime and costly repairs.
- Reduced Costs: Digital twins can be used to test new configurations and scenarios without the need for physical testing, reducing costs and speeding up development times.
- Improved Safety: Digital twins can be used to simulate dangerous scenarios, allowing organizations to identify potential hazards and improve safety measures.
The Future of Digital Twins
The use of digital twins is expected to grow rapidly in the coming years, as more organizations recognize the benefits of this technology. According to a report by MarketsandMarkets, the market for digital twins is expected to reach $15.66 billion by 2023, growing at a compound annual growth rate (CAGR) of 37.8% from 2018 to 2023.
As the technology continues to evolve, we can expect to see even more advanced applications of digital twins in industries such as transportation, energy, and construction. With the ability to simulate and analyze real-world scenarios, digital twins have the potential to transform the way we design, build, and operate complex systems.
Digital twin technology is rapidly gaining popularity in the industrial sector, offering many benefits such as improved efficiency, better predictive maintenance, reduced costs, and improved safety. As the technology continues to evolve, we can expect to see even more advanced applications of digital twins in a wide range of industries.